During the first week I’ve learnt that the pitfalls of CFD are many, and that I’m a complete amateur at it. I understand the basic concepts, such as meshing, finite element method etc. This isn’t good enough to create a simulation that will correspond to reality however. For now, questions like “How do I define the size my mesh should have?” and “What numerical solvers are used and how does that affect the result?” will remain unanswered. There will be a lot of reading and understanding maths ahead.
Week 1
This week I started work on my bachelor thesis. I’m working together with a friend from both previous courses and AESIR. Our goal is to simulate a swirl injector for ethanol in a small rocket engine.
The idea is to use CFD (Computational Fluid Dynamics) to simulate the swirler. CFD is quite similar to the Finite Element Methods used for simulating material stress in solid mechanics. The caveat is that in fluid mechanics things tend to move, and the properties of the fluid can change depending on what type of flow you have, so there’s way more equations to solve.
As part of our thesis we will do a litterature review, which is perfect since CFD is an active area of reasearch. Both in developing faster computing methods, and developing more accurate methods.
I’ll probably get more into detail in all of this as we go along, but for now this is what me and Dylan whent about in our first week.
Learning basics of CFD
CFD works on the basis on dividing a fluid flow into a mesh, usually into small segments of triangles or tetrahedrons (depending on if you’re working in 2D or 3D). You can then describe how every element in the mesh will interact with the elements surrounding it. In fluid mechanics we can essentially think of it as a number of control volumes, and we write up the equations for how the flow/pressure/etc (essentially Navier-Stokes equations) in one control volume will affect these things in adjacent control volumes.
We’ll define boundary conditions in the mesh (essentially defining input/output elements and walls etc). The CFD solver will then attempt to solve these equations for all the mesh elements numerically. Once this is done, we’ll take a step forwards in time and redo the whole thing.
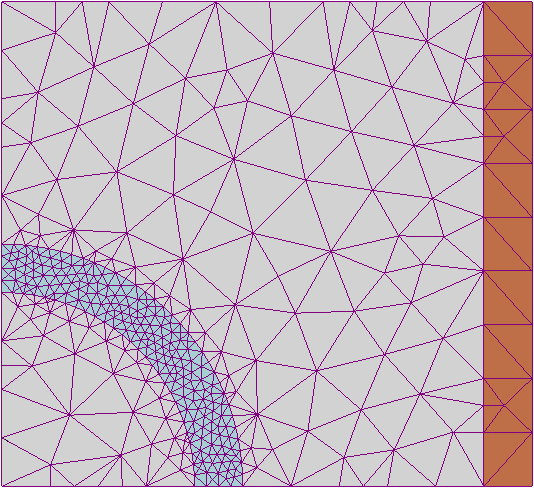
For those of you that have previously solved differential equations numerically this should sound very familiar. The tricky thing here is that in CFD we’ll have multiple things to solve for, and different solvers might solve pressure first, or velocity and so forth. Another thing to watch out for is the sizing of the mesh. Especially close to “tricky” boundaries, we’ll have to increase the resolution of the mesh to achieve a sufficiently correct solution.
Understand that my understanding of CFD is still somewhat lacking, so I might have gotten something wrong here. For now, I’ll have to go back and brush up on some of the differential equations math I did last year, as well as read more into the math behind different solving methods.
Learning Ansys
This took quite some time, but not for the reasons I expected.
The program we have abailable to us (through university) that can do CFD simulations is Ansys. It’s a full fledged suite for a lot of engineering work and simulations. For now I’ve just followed some easy tutorials and made a 2D flow simulation of von Karman vorticies. Just so I get used to the interface. This took quite some time, but not for the reasons I expected. Setting up the actual simulation was fairly easy, drawing a rectangle with a circle inside it using Ansys CAD interface was not.
For now I don’t really care about making an accurate simulation or what all the options actually do, I’m just getting used to the workflow. I’ve also concluded there are a lot of different options when doing CFD simulation, and you really need to know which one to use depending on what kind of problem you’re working with. In conclusion, these kind of things aren’t something you would trust an amateur to do and actually come up with a simulation that corresponds to reality. I’m clearly on the amateur side of things (for now).
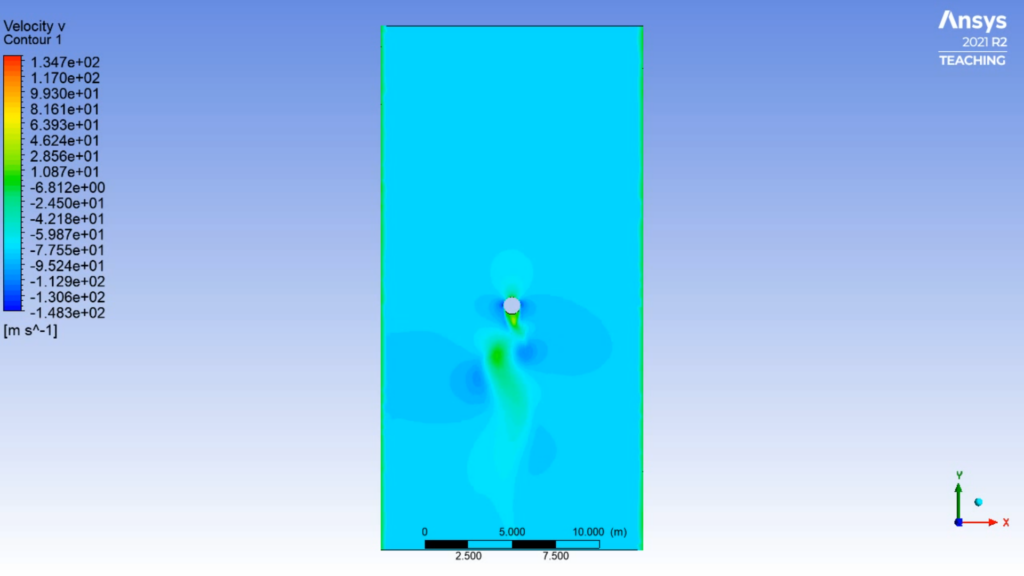
Planning
Any good project starts with a plan. Because we’re both beginners to CFD, we’re expecting the unknown pitfalls to take up a lot of our time. As such it is actually quite hard to make a good timeplan. For now we’ve written down a list of things we know will be needed for the actual simulation, like creating a CAD model, creating a mesh to do the simulation in and learning the basics of how CFD works (basically learn some of the maths behind the scenes).
We’ve also included some items for our litterature review. For now it seems like there’s two routes we can choose here. Either more method oriented and learn about CFD solvers and methods as well as what kind of problems they’re good for. The other option is to look more at what work has been done om swirl injectors ethanol combustion. We’re going to have to ask our assistant teacher about this.